

- #Pro ii simulation manual manual
- #Pro ii simulation manual software
- #Pro ii simulation manual Pc
- #Pro ii simulation manual plus
#Pro ii simulation manual plus
Aspen Plus DynamicsĪn Aspen Technology Inc. Learn more about Aspen Custom Modeler at Aspen Technology Inc. To use Aspen Custom Modeler, log on to your account and click the following: "Start-Programs-ChemEng Applications-AspenTech". You can then use instances of these models in Aspen Plus or Aspen Dynamics simulations.
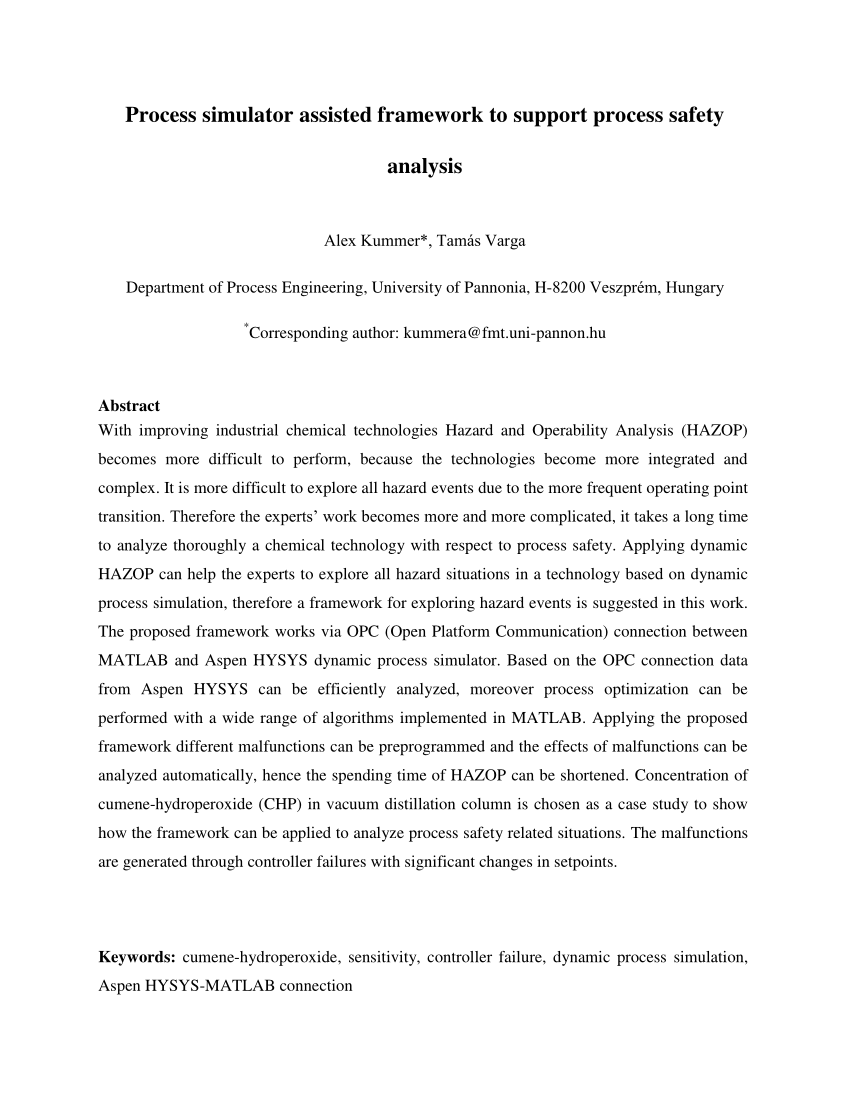
#Pro ii simulation manual software
erosion) Identify unacceptable temperature profiles / temperature approaches Integrated reporting (All Unit Ops / H&MB) in one place Thermodynamic models and data seamlessly match up with as-built geometry and process conditionsĢ1 Where do we go from here? Provide Feedback to the Software Vendor(s) Rigorous Simulation Go Faster! Stability Improvements needed for complex flowsheets Provide hidden workaround when HTRI unit operation encounters fatal error Simplicity for invoking HTRI (toggle back and forth) Kettles / Thermosyphon (flowsheet communication, detailed piping, etc.Create custom models of virtually any system described by nonlinear differential and algebraic equations. LMTD = U = 17Ģ0 Benefits Screen for damaging flow-induced tube vibration or acoustic resonance at higher flowrates, different feeds, other Dynamic pressure impact to equipment (rho-v2 i.e.
#Pro ii simulation manual manual
As-Built hardware is expected to meet / exceed duty within hydraulic limits Each service designed as a discrete unit operation MANUAL Steps to move Data No check of impact to the overall system through rigorous flowsheet modeling of vendor supplied equipment No FEEDBACK Mechanism Unexpected performance may result from as-built accumulative overdesign and variance from design temperature / pressure profiles Process Data Design Conditions Materials of Construction Heat Transfer Data Sheet Setting Plan Mat l Requisition Installation Startup Operation Troubleshoot 4ġ2 Cold Box Simulation Xpfe Simulation checks profiles, integration effectivenessġ3 PRO/II - HTRI (Xpfe ) Integration (This is Significant) Stand-alone modeling of a single unit operation PRO/II links Xpfe via CAPE-OPEN Xpfe is not connected to other flowsheet elements does not exchange data or contribute to the main flowsheet solution CAPE-OPEN Unit Operations calc s occur after flowsheet solves Stand-alone modeling of a Cold Box exchanger train looks promising Still in early stages of testing, implementation, and validation SIGNIFICANT time savings for engineers 13ġ4 PRO/II - HTRI (Xpfe ) Integration (This is More Significant) Integrated modeling PRO/II links Xpfe via CAPE-OPEN (same as stand-alone) Xpfe is fully connected to other flowsheet elements Xpfe Unit Operations calc s occur as flowsheet solves Integrated modeling of Cold Box exchanger train is challenged Fails to solve in some cases Could be operator error but robustness / stability should be investigated by software vendors to improve Opportunity for SIGNIFICANT time savings for engineers 14ġ6 PRO/II - HTRI Integration - What are the Benefits? Energy / Margin Credits (% OPEX, CIT, other) Process Optimization and Improved Integration of Exchanger Networks Species Targets (H2, other) U x Surface Area (UA) = Opportunity Property Generation is freaky fast Facilitates what if analysis Analysis for Fouling Modeling / Reduction Benefits from combination of integration / rigorous modeling 16ġ7 Optimize Heat Exchanger Design in the Network Basic design know the parameters! Q = UA (f) LMTD Q = duty U = overall heat transfer coefficient A = surface area LMTD = Log Mean Temperature Difference Pressure Drop Inside tube heat transfer coefficient (h i ) for turbulent flow inside tube varies ~ m 0.8 ΔP varies ~ m 2 A realistic pressure drop should be determined at this stage to avoid re-work Fouling predictive models may include pressure drop as one of the mitigating parameters i.e.
#Pro ii simulation manual Pc
2 Linking Third Party Software Heat Exchanger Network Simulation 2014ģ Process Heat Transfer Modeling - Perspective Fouling Factors Established Kern, McAdams, Tinker, Bell-Delaware First TEMA design methods are published to members HTRI Founded Delaware Research Project issued Final Report HTRI Publishes Stream Analysis Method (Tinker) Programmable, electronic desktop calculators become affordable Apple Computer Introduces Apple I personal computer (4K memory) Most PC s provide 32K chip memory allowing program design methods 1987 HTRI releases first PC version of Shell & Tube software 1990 s Property Generation from a stream in PRO/II to HTRI HEXTRAN makes it possible to analyze complex heat exchanger Networks Process Simulators linked to 3 rd Party Specialty software 2015 (?) Specialty 3 rd Party Software embedded in Process simulators to permit rigorous modeling of process equipment 3Ĥ The heat exchanger design process Design is based on specified process conditions, materials, fouling factors, etc.
